Det Energipolitiske Udvalg 2010-11 (1. samling)
EPU Alm.del Bilag 285
Offentligt
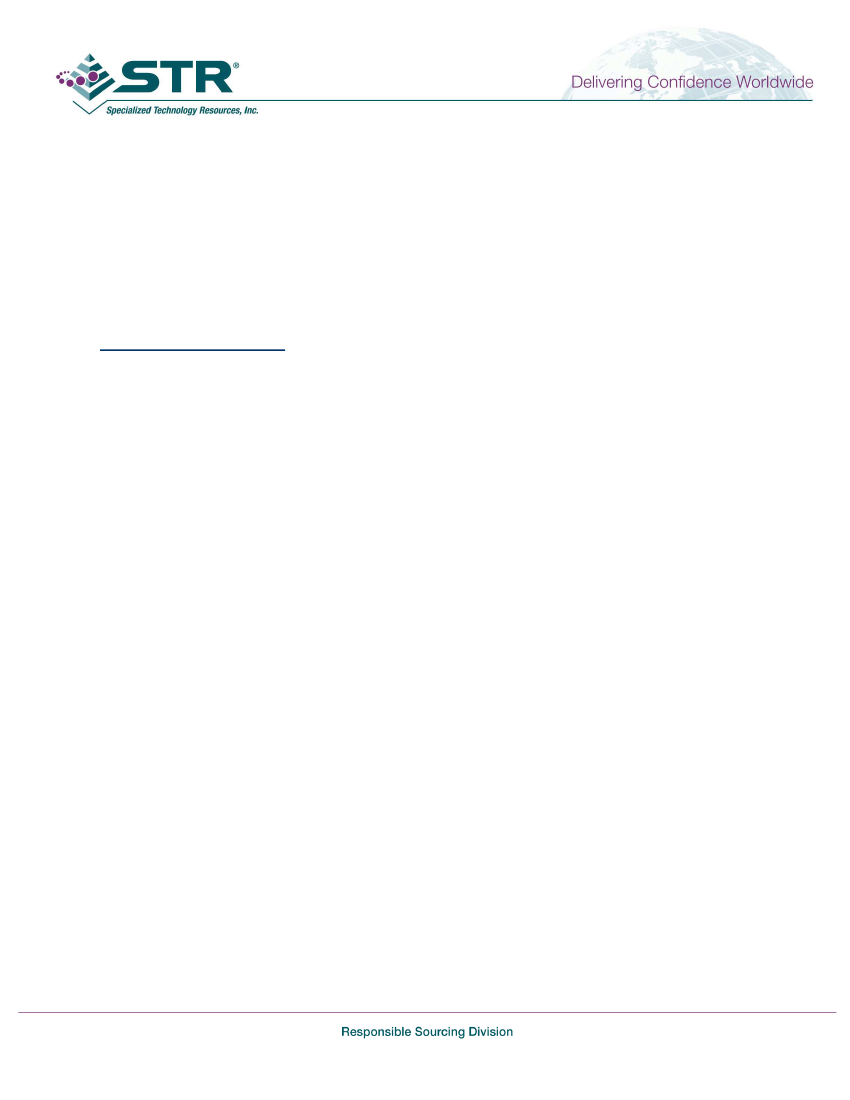
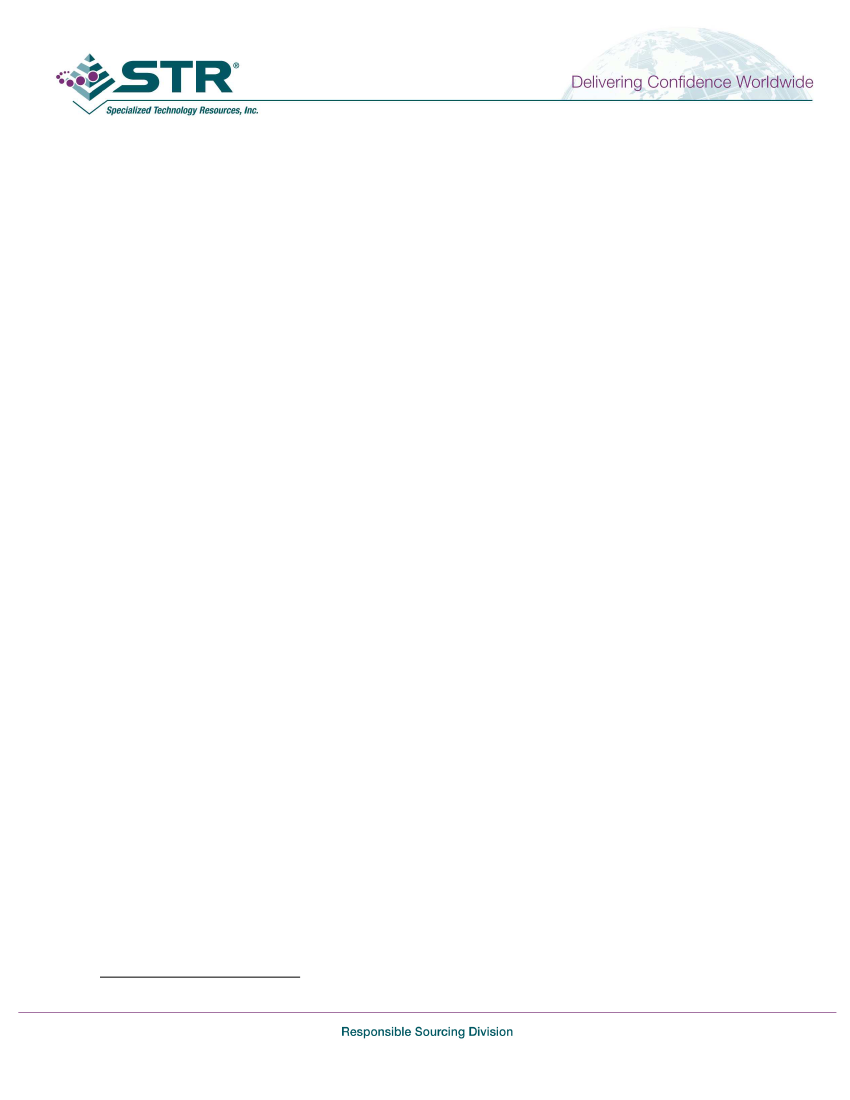
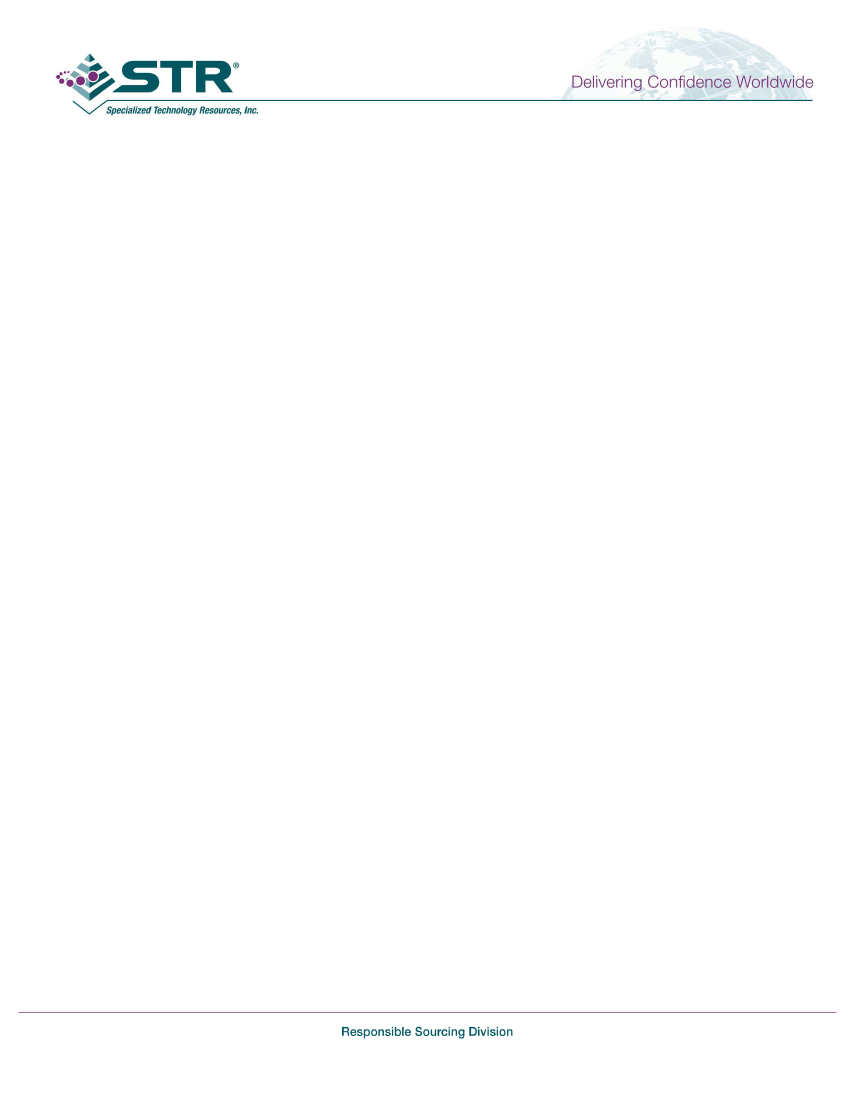
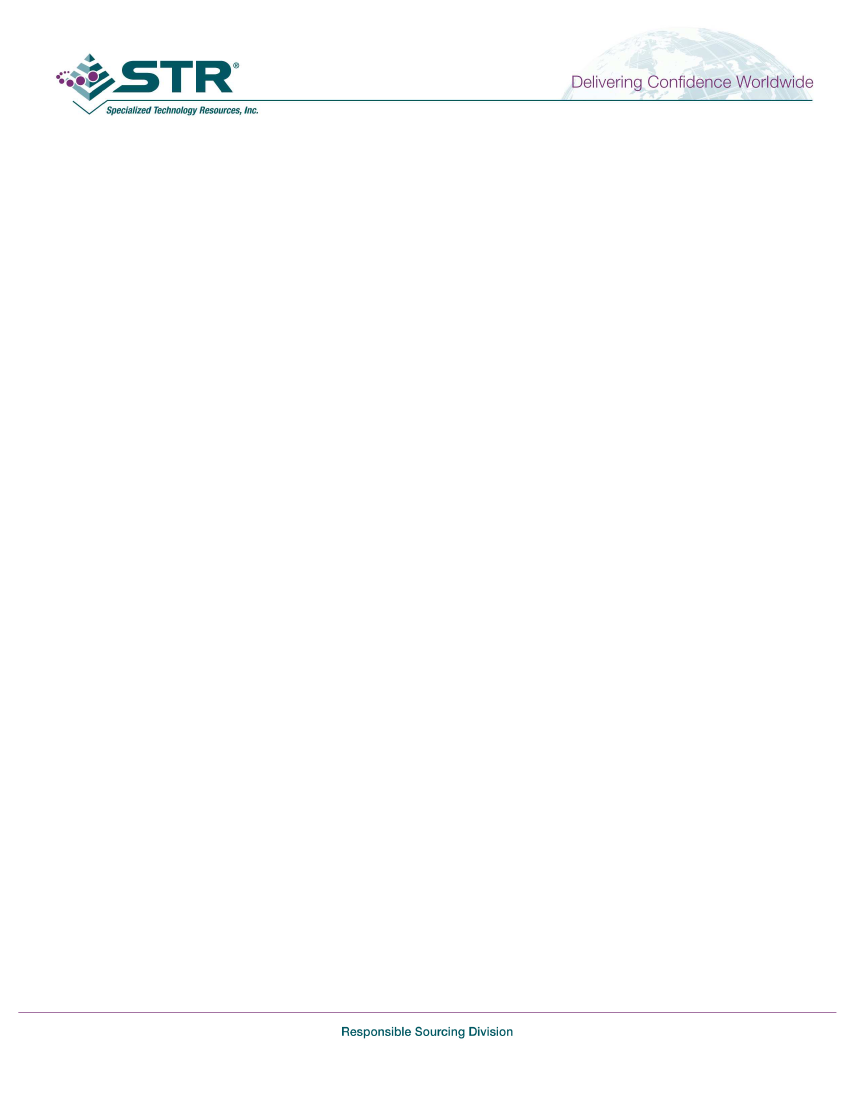
STR-RESPONSIBLE SOURCING
DONG ENERGY CODE OF CONDUCT ASSESSMENT REPORT
OJSC SUEK (SIBERIAN COAL ENERGY COMPANY)
APRIL 18, 2011 (REV. JUNE 8, 2011)
EXECUTIVE SUMMARY
OJSC SUEK (Siberian Coal Energy Company) is the largest thermal coal producer and energyenterprise in the Russian Federation, and has affiliates and subsidiaries in the Republic ofBuryatia, Kemerovo Region, Krasnoyarsk Region, Primorsky Territory, Khabarovsk Territory,the Republic of Khakassia, Zabaykalye Territory. SUEK is one of the coal suppliers to DONGEnergy. In December 2010, specific allegations against SUEK as one of DONG Energy’ssuppliers were published in Danish media related to working conditions at SUEK undergroundcoal mines in the Kemerovo region.On the basis of the serious accusations raised by Danish media, DONG Energy requested anextraordinary third party assessment of working conditions of its coal supplier SUEK in Russia.Specialized Technology Resources’ Responsible Sourcing Division (hereinafter referred to as“STR-RS”) was selected by DONG Energy to perform the assessment. The assessment wasconducted from March 21, 2011 to March 30, 2011 by a four-person team of social auditors andan external specialist in environmental, health and safety in the mining industry.The assessment of SUEK mining operations covered SUEK’s headquarters in Moscow, SUEK’sKuzbass office in Leninsk-Kuznetsky and three of SUEK’s underground mines producing coalfor export in the Kemerovo region which is delivered to DONG Energy.Besides the STR-RS assessment team, two representatives from DONG Energy visited thearea and one of the underground coal mines in the period from March 21, 2011 to March 23,2011 to get an overview of mining industry in Russia and to discuss the issues raised by Danishmedia.The methodology used for the assessment consisted of site visits and observation, interviewswith employees, management, and stakeholders and documentation review. The assessmentteam engaged a variety of stakeholders, including the Russian Independent Union of CoalIndustry Workers, Kiselevsk territorial division of Russian Independent Union of Coal Industryworkers, the South Siberian Division of the Federal Service of Ecological, Technological andNuclear Control of the Russian Federation (RosTechNadzor, the Russian Federal Mining andIndustrial Inspectorate), State Labor Inspectorate in Kemerovo Region, City administration ofLeninsk-Kuznetsky, Scientific - Clinical Center for Protection of Health of Coal Mining Workers,Biodiversity Conservation Center, Ingortech (company that installs methane monitoringsystems), and the Head of the Coal and Energy Department of the Kemerovo region (via letter).
The standards of measurement used in the assessment included DONG Energy’s Code ofConduct for Suppliers, national laws and regulations of the Russian Federation, and ILOConvention 176 concerning Safety and Health in Mines (1995)1. Reference standards, used toidentify best practices, included the International Finance Corporation (IFC) PerformanceStandards and the World Bank/IFC EHS Guidelines for Mining.SUEK’s compliance with national and international standards was assessed in the areas oflabour conditions, occupational health and safety, and environment. In the course of theassessment, the team observed that SUEK has developed and introduced an integratedmanagement system, in order to ensure compliance of all SUEK enterprises with theinternational standards in the sphere of quality management, environmental management andmanagement of industrial safety. An ISO 9001 certificate for SUEK; and ISO 14001, OHSAS18001, and ISO 9001 certificates for SUEK Kuzbass issued by Afnor Certification were providedfor review.The assessment team did not observe any evidence of child labour, forced labour,discrimination, harassment and restrictions to freedom of association practiced in regards ofemployees. However, a number of issues were discovered in the areas of timekeeping andwage calculation. During the visit to the coal mines, the assessment team observed thatregulations accepted and adopted at the level of Headquarters were not understood or fullyimplemented by the management at the level of the mines. The timekeeping system was foundto be not fully transparent which presented limitations in determining compliance with Russianlegal regulations and binding collective bargaining agreements. As such, the assessmentidentified several concerns related to working hours and compensation including provision ofinsufficient weekly rest to employees, non-compensation of overtime work, insufficientcompensation for employees travelling from the surface of the mine to the working areaunderground.In the newspaper article published in Danish media in December 2010, SUEK’s wage systemused for underground workers was criticised for being structured in a way that encouragesemployees to take major safety risks by, for example, manipulating methane monitoringequipment. Since the wages depend on production volume, the employees may neglect safetyprocedures that would slow down or suspend operations in order to earn enough money tosupport themselves and their families.In January 2011, an amendment to the Federal Industry Agreement on the Coal Industry of theRussian Federation for 2010-2012 was incorporated at the mine level. The RussianIndependent Union of Coal Industry Workers reached an agreement with the representatives ofcoal mining companies in Russia, establishing that the fixed amount of the wage should not beless than 70% and that the variable component of the salary should be not more than 30%.SUEK has signed this collective bargaining agreement. In the course of the assessment, it wasobserved that the new requirement regarding the components of the wage, aimed to reduce thedependence of employees’ wages on the productivity, was not fully implemented throughout theentire company as the compensation method for underground employees practiced at all threemines was still based on production volume (the amount of coal extracted by one team in onemonth), rather than an hourly rate.
1
Russia has not ratified this Convention.
By maintaining a wage system which depends on the production volume, the management isable to potentially motivate employees to continue working under dangerous conditions if thelevel of methane exceeds permissible limits because termination of the work would result in theloss of productive work for employees, which in turn, affects employees’ wages.During the assessment, it was observed that, from a technical standpoint, SUEK managementuses several measures to prevent accidents, including investing in modern methane monitoringsystems. However, as pointed out by external experts, it is still possible for employees tointerfere with the system in order to prevent it from turning on the alarm and shutting offelectricity if the level of methane increases.There was no evidence detected during the assessment that the management did not allowemployees to report on dangerous situations or obliged them to stay at their work places if thelevel of methane increased. Thus, the only reason why employees would want to tamper withthe methane detectors would be the fact that the employees’ wages depend on the productionvolume.Taking into consideration the dangerous nature of the work and the possibility of interfering withthe methane monitoring system, it was recommended to withdraw modify the system ofremuneration that completely or partly depends on production volume in line with therequirements of the Federal Industry Agreement on the Coal Industry.With regards to internal grievance mechanisms, SUEK has an internal grievance procedure inthe form of a suggestion box, placed at the entrance to the building (office and other services).At the same time, the grievance procedure does not include registration of complaints at thelevel of the mines and also does not include a response procedure.Although there is a formal written procedure that determines SUEK’s community engagementstrategy, in practice, the activities in this area are limited and does not include identifying andmitigating risks and impacts of the company’s operational activities on the surroundingcommunities.Auditors were not provided with any samples of registered complaints orconfirmation of the response procedure.During the assessment it was observed that SUEK is familiar with local legal requirements onoccupational health and safety, protection of the environment and strives to ensure compliance.SUEK has competent personnel responsible for occupational health and safety andenvironment at the Headquarters, at the regional office (SUEK Kuzbass) and at each mine. Theassessment team did not identify any practices that did not conform with the employer’sresponsibilities under ILO Convention 176, however, a number of minor occupational health andsafety concerns were observed during the assessment.According to documents reviewed, (investment plans for each mine) and as per SUEKmanagement, SUEK has invested over US$289 million since 2005 in the improvements ofoccupational and industrial safety at its enterprises. Organizational measures include expensesfor medical examination for employees, H&S trainings, and risk assessments, among others.Technical measures cover expenses for ventilation system of the mines, measures againstmethane and coal dust, fire safety, measures against noise, vibration, excessive temperatures,improvement of lighting at workplaces, and others.
The management also provided data on planned investments in occupational and industrialsafety for 2011 for review. SUEK is planning to invest a further US$45 million) in itsunderground coal mining enterprises in different regions.DONG Energy provided SUEK the possibility to review the assessment report and comment onthe findings and observations made by STR-RS auditor team.SUEK had objections with regards to two of the findings on working hours and remuneration.DONG Energy and STR-RS are in a dialogue with SUEK with regards to interpretation of theassociated legal requirements for the two disputed findings and with regards to corrective actionplans for the remaining findings.At this stage, STR-RS has not verified actions which have already been implemented by SUEKsince the assessment since the company has not provided supporting documentation or otherevidence of implementation. However, a re-audit of the company is planned in order to verifycorrective actions and progress at the company within the next 12 months.